PETRONAS’ largest downstream greenfield development is on the verge of takeoff. Five years in the making, the USD27 billion, 6,303-acre Pengerang Integrated Complex (PIC) is anticipated to lead PETRONAS’ charge towards its net zero carbon emissions (NZCE) 2050 aspirations upon its start up in 2021.
10/02/2021 • 8 mins read
The Pengerang Integrated Complex
Designed with sustainability in mind.
Chai Li Tiing and Angeline Lim
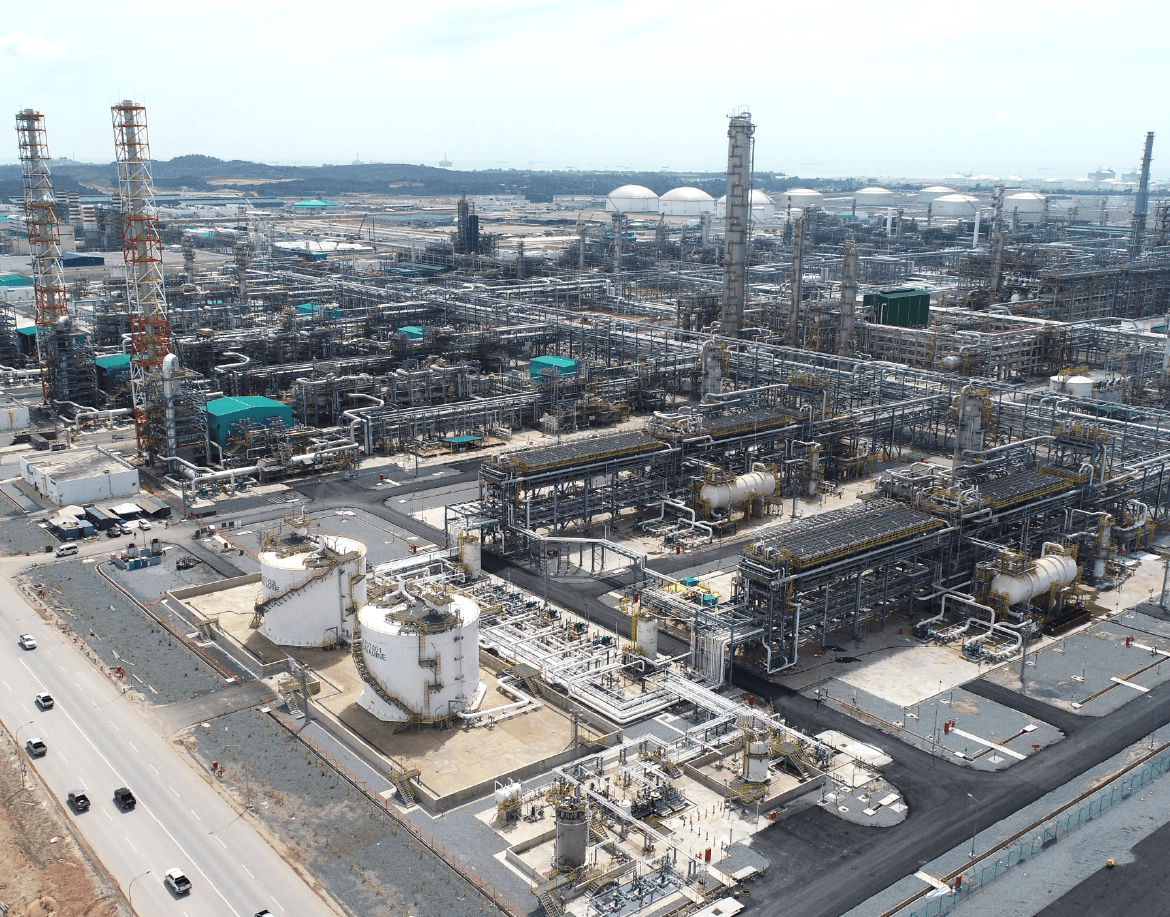
“When the idea for the complex was conceived about 10 years ago, there was already a strong vision of sustainable development,” says Ir Dr Colin Wong Hee Huing, former Senior Vice President and Chief Executive Officer of PETRONAS Refinery and Petrochemical Corporation (PRPC), who led the Pengerang Integrated Complex development until his retirement at the end of 2020.
Sustainability cuts across the blueprint of the PIC and is deeply embedded in its operational and management practices.
“It is focused on fully capitalising on its design advantage, delivering clean energy and low carbon solutions to build a sustainable business on the back of operational excellence. Guided by the PETRONAS Sustainability Agenda and the NZCE aspirations, I believe we are on track to embed sustainability principles across all areas of the business. This way, the balance between ‘Profit’ on one hand, and ‘People and Planet’ on the other, becomes ingrained, organic and second nature,” he adds.
World Class Efficiency and Sustainability
Unprecedented in its scale and complexity, PIC is ranked among the world’s best. The Nelson Complexity Index (NCI), a metric based on complexity, replacement costs and relative value-adding capability, places the PIC Refinery at 9.48, and the Refinery and Petrochemical Integrated Development (RAPID) at 12.03.
“This is comparable with world class facilities and we are well-positioned to extract maximum value from oil and gas resources,” says Wong.
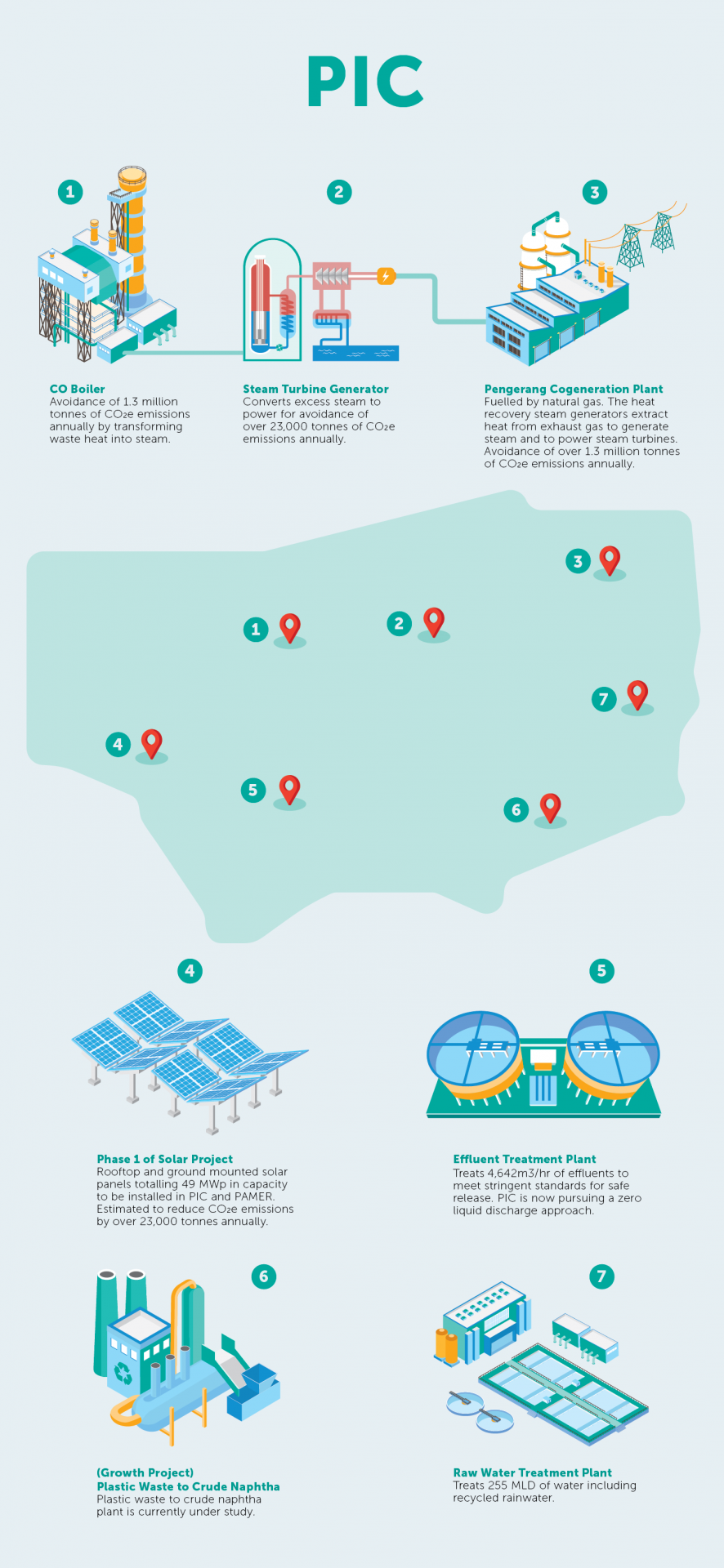
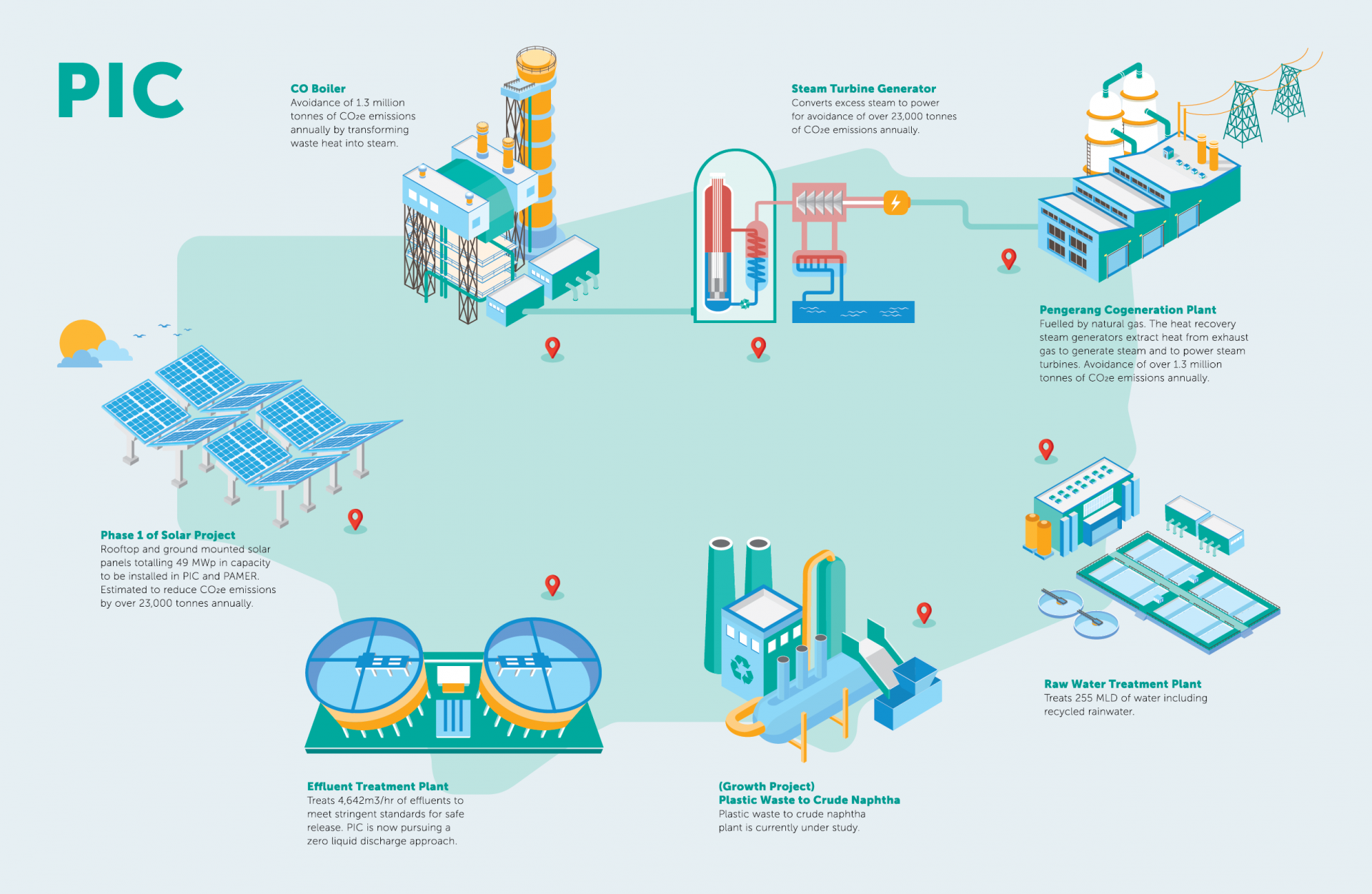
It is this level of complexity and integration that sets PIC apart from other complexes. Its Refinery, a sour full conversion facility that produces fuels like low sulphur diesel, jet fuel and motor gasoline, is the primary feedstock supplier to the Steam Cracker Complex (SCC) and the Petrochemical Complex. These three complexes are supported by Associated Facilities that ensure PIC’s operational self-sufficiency and reliability.
The complex is powered by the largest and most efficient power plant in the region – Pengerang Cogeneration Plan (PCP) that is fueled by natural gas, a move towards cleaner fuels. Other supporting facilities include an LNG regasification terminal, an air separation unit, common utilities and offsite facilities, water supply facilities, solid product handling facilities and jetty, and a liquid bulk terminal with storage facilities for crude, petroleum products and petrochemicals.
Engineering design optimises every molecule for best possible returns and ensures the highest plant and energy efficiencies to minimise carbon footprint.
The PCP’s design incorporates Heat Recovery Steam Generators that extract waste heat from exhaust gas to generate steam for process purposes and to power steam turbines, contributing about 1.3 million tonnes per year in CO2e emissions avoidance.
The cogen plant provides high reliability of supply at relatively low generation cost, supplying 1,300 MW of 275 KV power and 1,300 tph of high pressure steam to PIC facilities, with 600 MW of power exported to the national grid.
In the Residue Fluid Catalytic Cracker (RFCC), the CO Boilers transform waste heat into steam for process heating and to power turbines. The regeneration of RFCC catalyst produces a lot of hot flue gases and these convert boiler feed water into superheated steam for process use. This feature trims CO2e emissions by over 1.3 million tonnes per year. This massive heat recovery from hot flue gases via the CO boilers generate more than 700 tph of HP steam internally in Refinery.
In addition, a low pressure steam turbine generator converts all available excess low pressure steam to power, generating 12 to 20 MW of electricity that contributes more than 23,000 tonnes per year of CO2e emission avoidance. The energy in the excess LP steam would otherwise have been wasted through condensation.
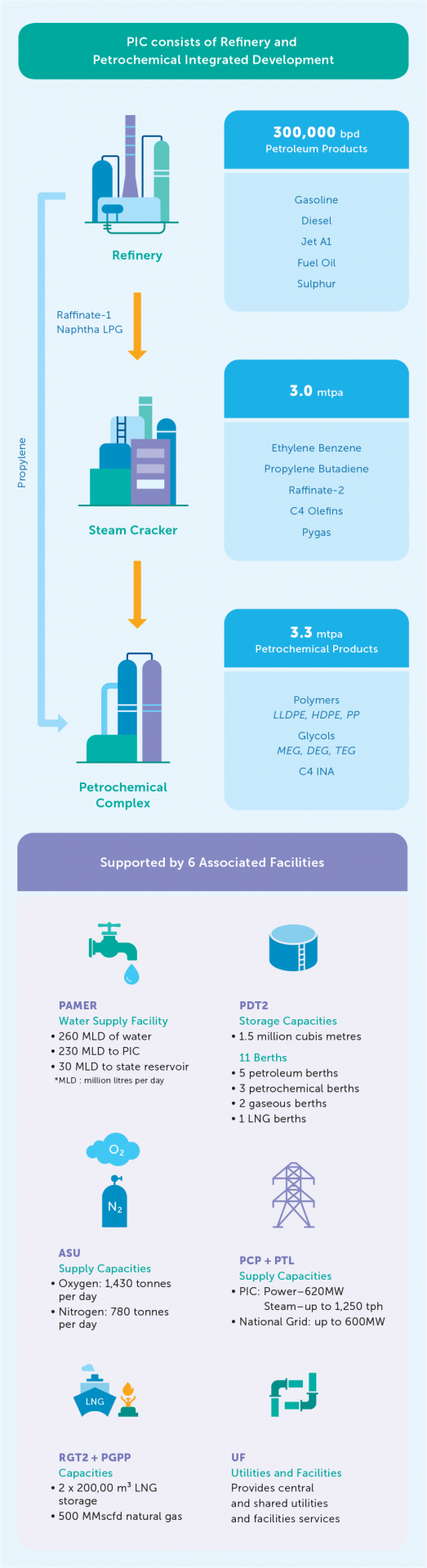
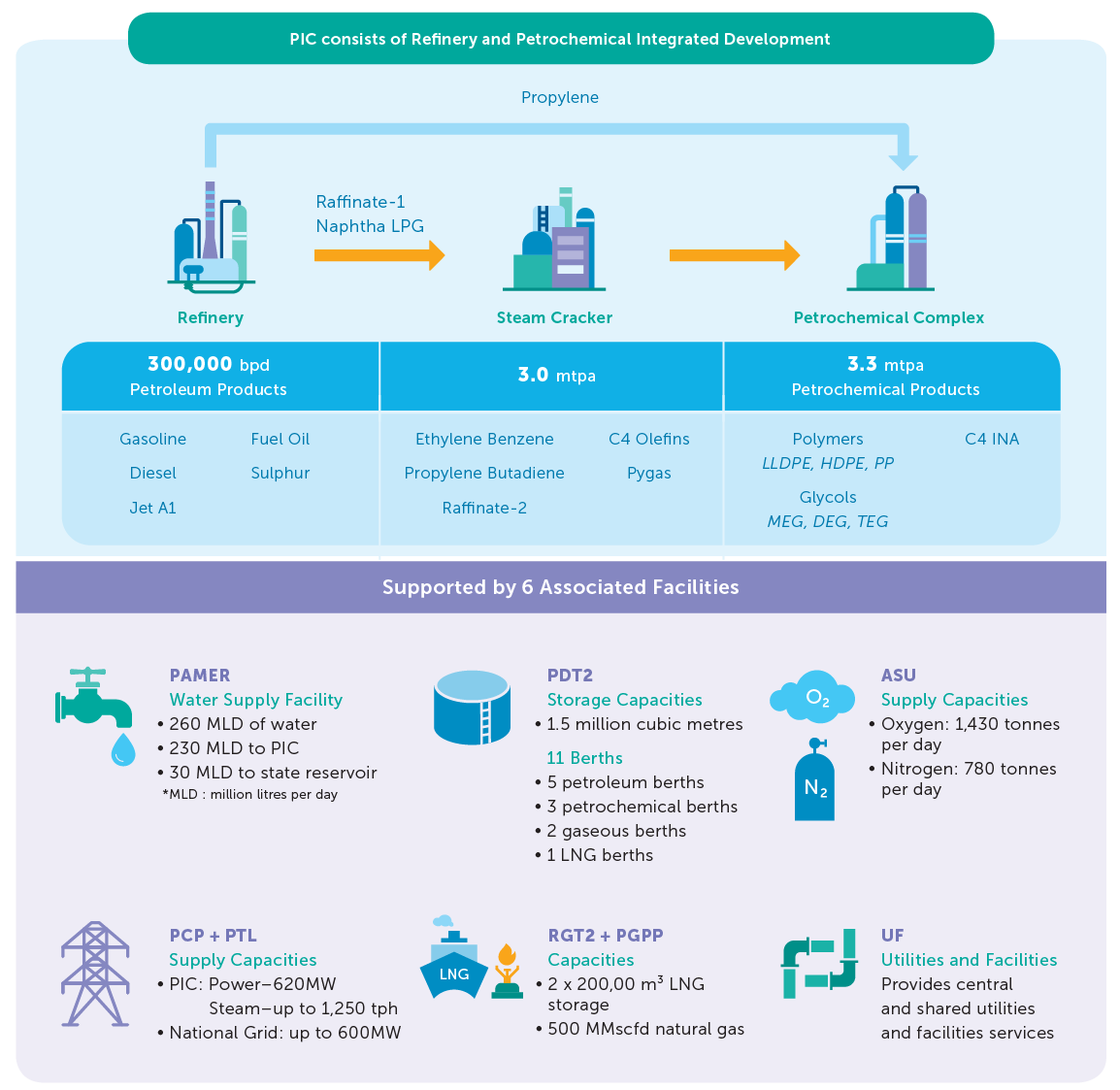
“By incorporating proven technologies and advanced engineering design, PIC delivers superior operability, with high efficiency and low carbon emissions, trimming Scope 1 emissions by 3.6 million tonnes, and enabling a reduction in carbon dioxide equivalent (CO2e) emissions by 26 per cent to 10.2 million tonnes annually,” says Wong, adding that PIC intends to continue keeping a tight lid on carbon emission levels park-wide.
When up and running, the complex would also help fulfill Malaysia’s requirements for cleaner and more efficient next-generation fuels and petroleum products. PIC’s Euro 5 specification gasoline and diesel meet extremely stringent emission standards, reflecting PETRONAS’ commitment to reducing emissions.
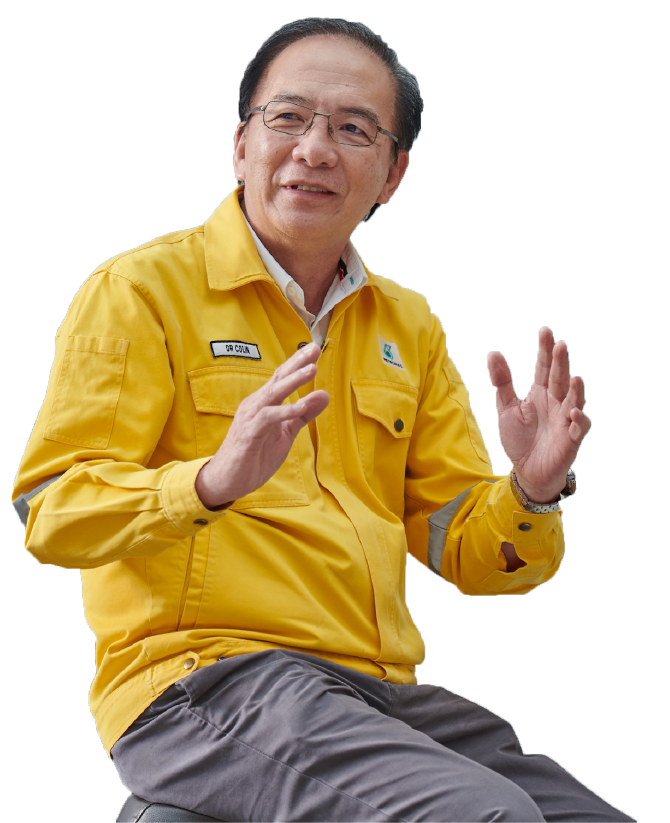
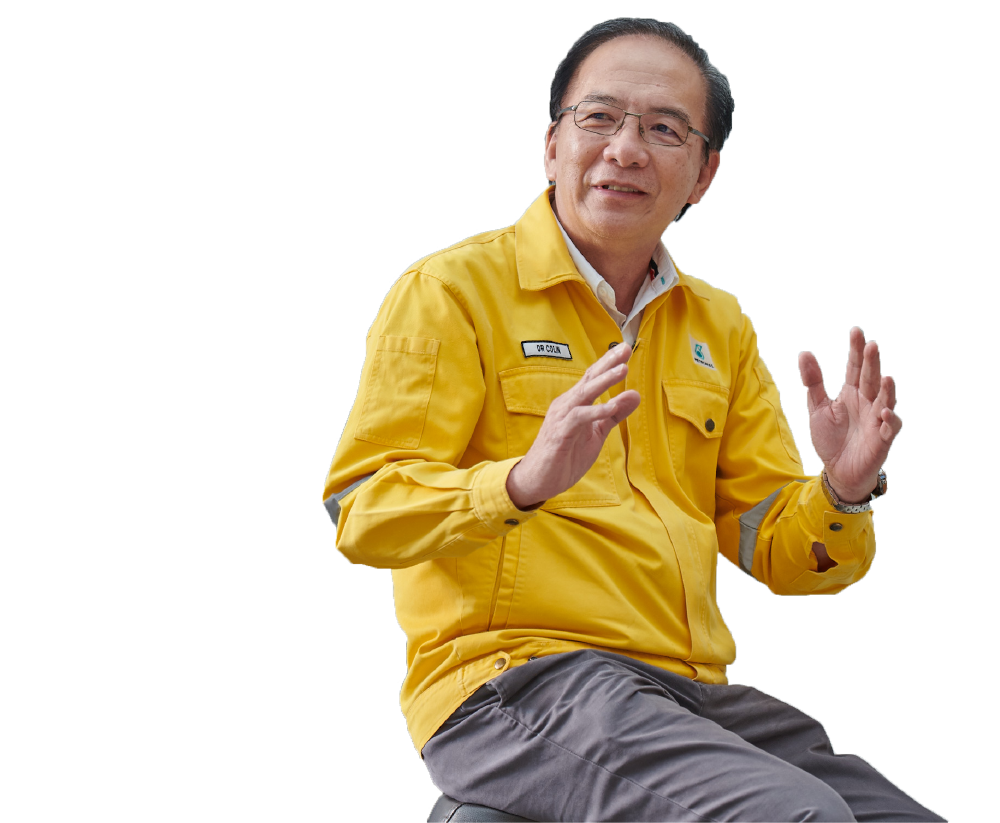
Ir Dr Colin Wong Hee Huing
Former Senior Vice President and Chief Executive Officer of PETRONAS Refinery and Petrochemical Corporation
Trendsetter for Sustainable Complexes
In addition to the facilities’ design, PIC’s management practices and innovative systems are all important components to propel PETRONAS towards its NZCE 2050 aspirations announced by President and Group CEO, Tengku Muhammad Taufik in October 2020.
“We are capitalising on energy-based offsets, such as operational excellence to achieve carbon emission reductions, and exploring renewables and low carbon solutions. We are also embarking on forest-based carbon offsets like tree planting in mangrove forests,” Wong says.
A PETRONAS in-house innovation, the Energy and Loss Management System (ELMS), helps the complex track energy consumption and minimise energy loss from process facilities. All fuel-consuming units like furnaces have an energy efficiency of up to 94 per cent – the best that can be economically achieved.
Variable speed fans used in most processes reduce energy consumption while maintaining better process stability. To minimise energy loss due to flaring, the Fuel Gas Recovery System (FGRS) was installed in the Refinery to facilitate zero flaring during normal operations. Low nitrogen oxide or NOx burners are used in all furnaces to minimise emission of greenhouse gases. The management has gone the extra mile to ensure that emissions from the Refinery and its associated facilities comply with Malaysian and International Finance Corporation (IFC) standards.
Furthermore, Digitalisation was embedded in the overall design and construction of the complex, providing transparency of plant operations, eliminating human error, increasing efficiency and cross-functional collaborations, and enabling analytics for data-driven decision-making.
“PIC’s sophisticated system of ‘digital highways’ span the entire complex, linked by a 500km fibre optic backbone. Plant assets are digitalised while sensors and measuring devices capture all essential data in real time,” Wong says, noting that this extensive range of integrated digital and automated engineering solutions enhance operations and provide full visibility of plant operational data.
PIC is also aggressively pursuing initiatives in responsible water management, low-carbon energy, circular economy and positive social impact.
“We have also established comprehensive PIC Park Rules and Guidelines to ensure responsible governance within the park. Having been gazetted as a Protected Area under the Protected Areas and Protected Places Act, the rules help ensure that tenants comply strictly with local laws and regulations,” Wong explains.
With more projects in the pipeline, Wong reveals that, “PIC will be scrutinising potential new projects through a ‘sustainability filter’, evaluating them against the PETRONAS Sustainability Agenda and NZCE strategies, with criteria like energy efficiency, carbon reduction technologies, as well as a shift to clean energy.”
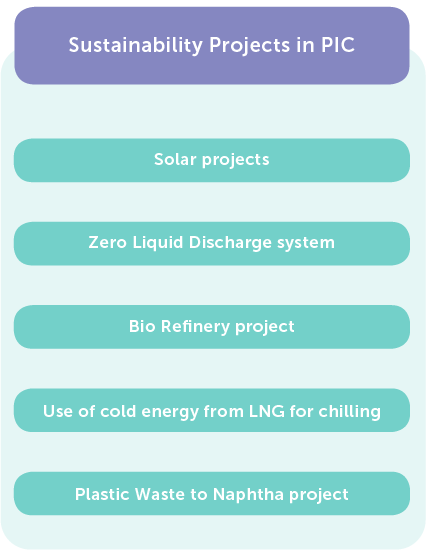

Powering on to Start Up
Safety is prioritised at the Complex, from the Project phase right through to Operations. A comprehensive assessment has been undertaken on design and engineering integrity, and operational readiness, to provide absolute assurance on safety and ensure a smooth start up in 2021.
A series of process safety trainings have also been rolled out to frontliners to establish strong ownership of safety procedures and maintain the highest safety standards. All PRPC staff including non-technical personnel attended the Safety in Operations training, with emphasis on the 8 Golden Rules of Process Safety and Zero Tolerance (ZeTo) Rules to cultivate a generative culture where everyone does the right thing all the time, even when no one is watching.
“We are fully committed to the highest levels of vigilance and safety, which has always been and remains our utmost priority,” Wong says. Besides ensuring that the facilities achieve stable operations safely, PIC is determined to stay laser-focused on operational excellence while pushing hard towards PIC growth.
With Wong’s retirement late last year, the baton has been passed on to Kamal Bahrin Ahmad, who will oversee PIC’s start up later this year. Coming into 2021, a year with persistent market turbulence, natural disasters in the form of a flood in the state of Johor and a pandemic that continues to rage, Kamal is determined to see PIC come to fruition despite the challenges.
There is an accelerated shift towards cleaner energy prompted by the drastic changes in the business landscape, notwithstanding the perfect storms of the COVID-19 pandemic and collapse in oil demand. And the push towards NZCE remains at the forefront of the agenda.
“In PIC’s Growth Masterplan for the next decade, sustainability projects are key. We will continue pursuing innovative ways to enhance our portfolio mix to remain competitive while contributing towards our NZCE aspirations,” Wong enthuses.
Echoing Wong’s sentiments, Kamal recognises the unprecedented circumstances at hand, “While many uncertainties continue to hang over PIC’s immediate future, the PETRONAS Group already has a plan clearly laid out as we march forward. With the unwavering determination and commitment of our teams, I believe we can successfully navigate these uncharted waters to conquer new frontiers.”
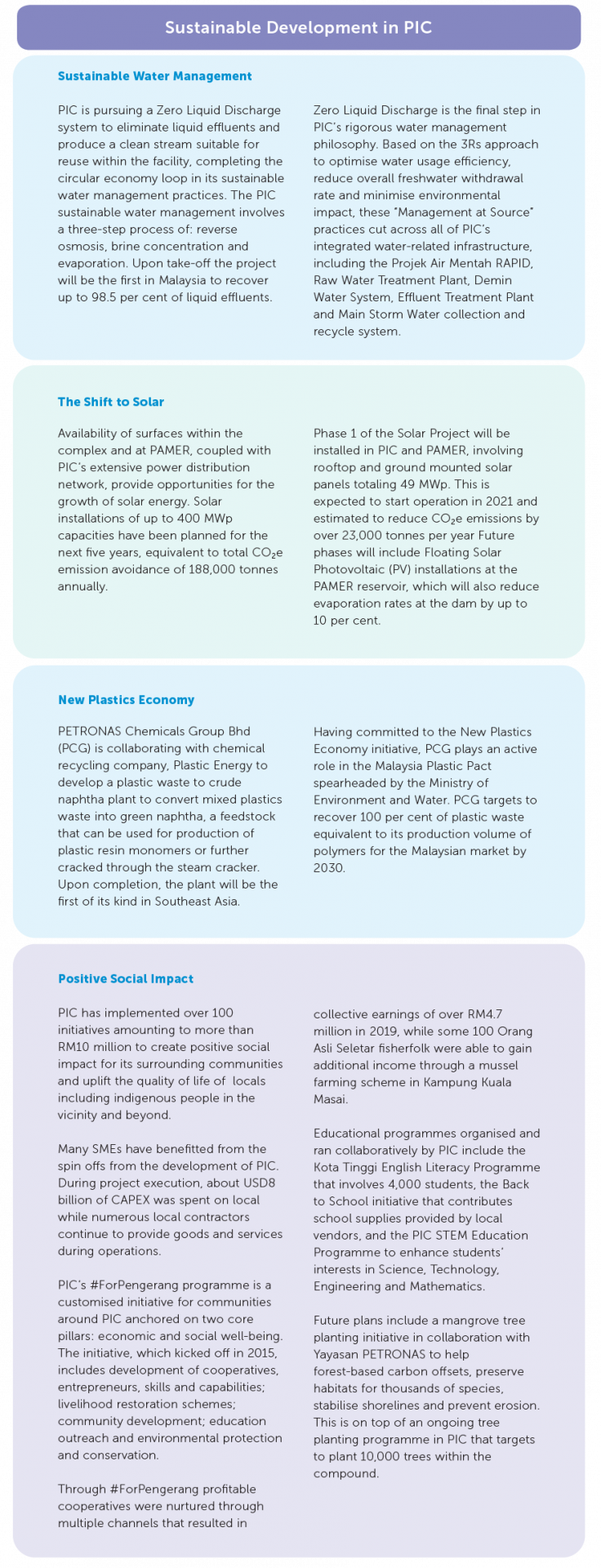
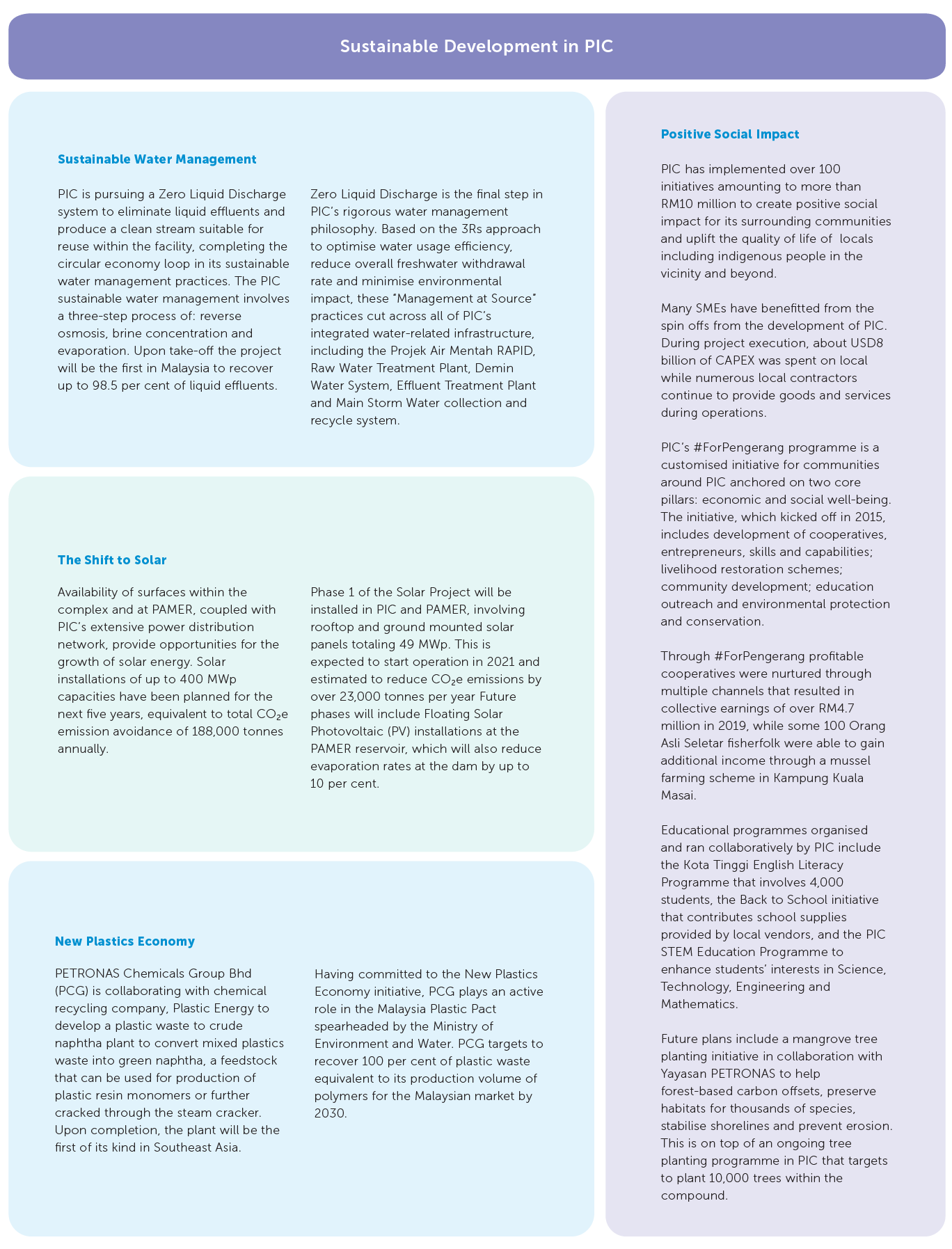